Prioritizing Racking Safety In The Modern Warehouse
Table of ContentsRacking Safety: How To Create A Culture Of PreventionCreating A Culture Of Warehouse Safety In copyrightImproving Warehouse Safety In copyright: A Comprehensive GuideOptimizing Safety In Warehouses With Data-driven InsightsRacking Safety And Warehouse Efficiency: Striking The Right BalanceWarehouse Safety In copyright: Case Studies And Lessons Learned
No issue how well carried out, an assessment will only be worthwhile if the problems noted by the group are meticulously taken a look at as well as appropriate rehabilitative activity is taken. The reporting and also the skill levels of the people given this responsibility will certainly vary from one company to the following, yet it is essential to keep in mind the following points when designating duty for reviewing assessment reports.At the very least among the persons in charge of examining assessment records should have the authority to take or figure out the needed rehabilitative procedures and to hand over that authority, as suitable. Specific problems may require the point of view of a specialist, such as an engineer or an industrial hygienist. It is important to inform those doing the assessments of any kind of follow-up steps that are to be taken, in order to improve their motivation.
It is equally as essential to guarantee that those who are in charge of performing evaluations get prompt feedback. Plainly, if there is no feedback or demo of rate of interest, they will quickly wrap up that inspections are a meaningless exercise. Lastly, information acquired from routine inspections should be subject to a detailed analysis in order to determine which areas need basic rehabilitative actions, and to identify fads as component of the performance bookkeeping program - Securite des palettiers.
Pallet Racking Inspections
Anybody accountable for accomplishing work area health and wellness inspections, especially work location health and wellness committee participants and also representatives, will certainly locate it helpful.
Health and wellness and also security boards can aid strategy, conduct, record as well as monitor evaluations. Regular office assessments are an important component of the general job-related wellness and safety program as well as administration system, if existing.
g., design controls, management controls, policies, treatments, individual safety devices) satisfy regulative and also management system requirements Planning is vital for an efficient assessment. Every examination has to examine who, what, where, when and also how. Pay specific attention to items that are or are more than likely to become harmful or harmful problems due to tension, wear, influence, resonance, warmth, corrosion, chain reaction or abuse.
Addressing The Top Causes Of Accidents In Warehouse Safety
Check out all workplace aspects individuals, the environment, the tools, the materials, and also the process. Individuals include the number of employees, demographics, change routines, as well as supervision. Environment consists of the office framework and setup, as well as the problems that surround the employees such as sound, resonance, lights, temperature level, as well as ventilation. Devices consists of machinery, devices, and apparatus for creating a product or a service, as well as security devices and personal protective tools (PPE) that may Securite entrepot be called for.
Process includes exactly how the employee interacts with the various other aspects in a series of tasks or operations. Threats can take place due to harmful office problems and practices including the office elements. Sorts of work environment dangers include: Safety and security risks such as those brought on by inadequate machine guards, harmful power (mechanical, electric, gravitational, pneumatically-driven, etc), cars, machinery , devices , absence of fall security , confined spaces , as well as home cleaning .
Chemical threats triggered by a strong, fluid, vapour, gas, dust, fume. or mist. Ergonomic hazards brought on by inappropriate work methods, inaccurate manual product handling , and poorly designed workstations, tools, as well as tools. These place physical (recurring as well as strong activities, uncomfortable stances, straining) as well as emotional (work, time pressure) needs on the worker that can bring about bone and joint injuries.
Warehouse Safety Inspection Services .
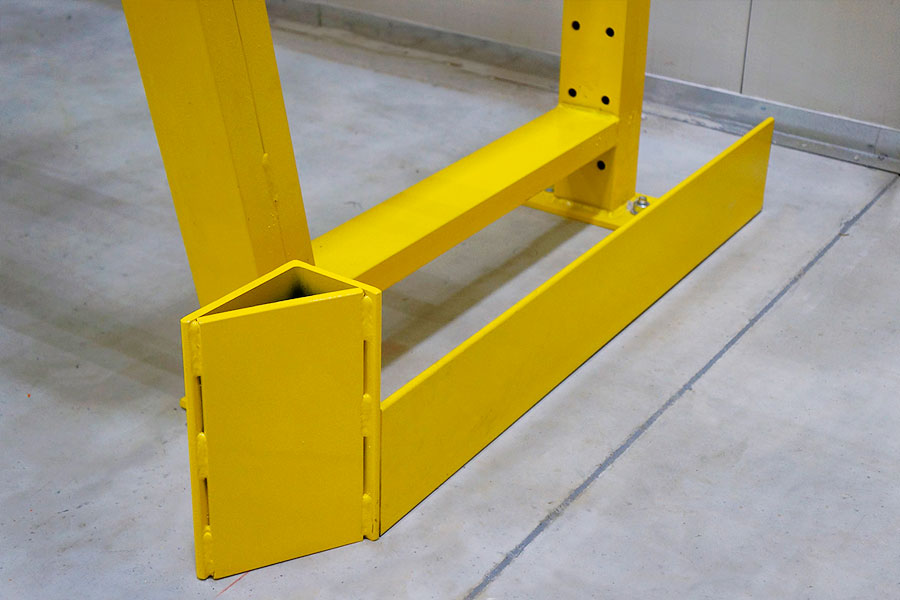
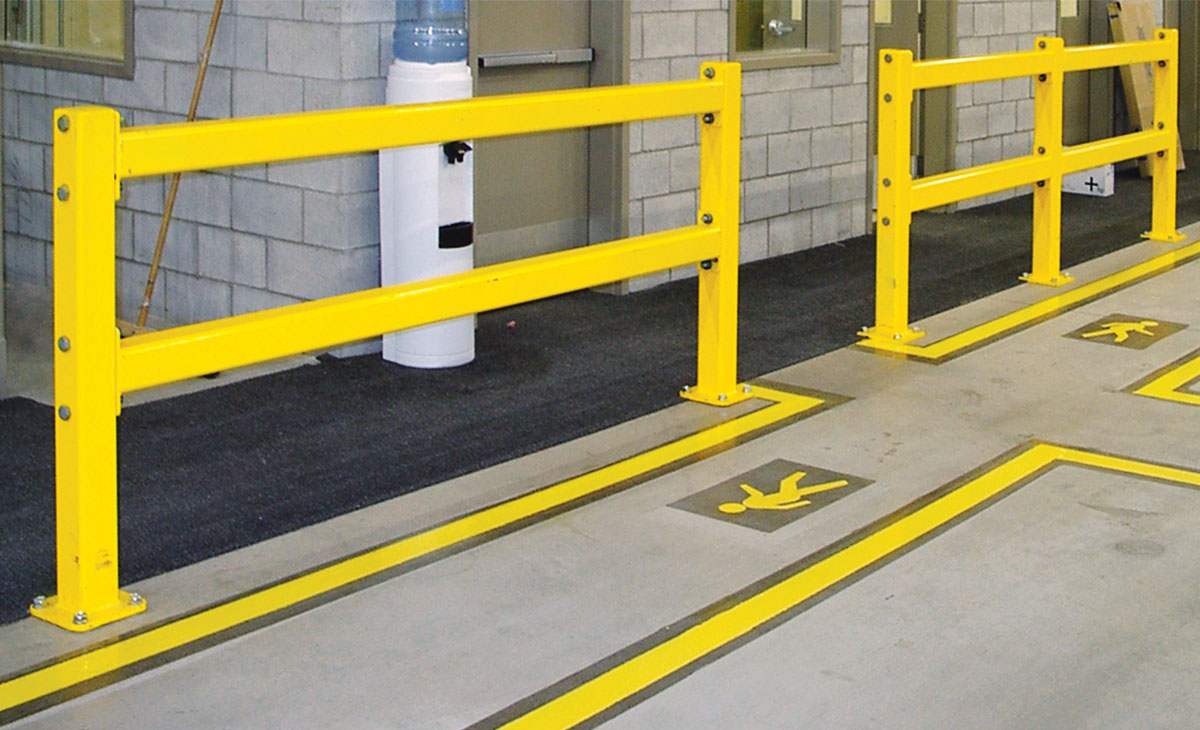
Read job area documents to come to be acquainted with the risks of the tools. Be conscious of any type of engineering security controls called for to securely operate the tools.
The Importance Of Racking Maintenance In Warehouse Operations
Check that all unsafe items are labelled suitably according to Work environment Hazardous Products Information System (WHMIS ) requirements. These files include workplace policies, guidelines and also policies, procedures, safe work techniques, emergency reaction strategies, records, and records. Being familiar with the typical secure operating conditions for the location can help inspectors to acknowledge hazardous deviations.
Do not permit the inspection team to end up being so objective on keeping in mind the details provided in the checklist that it misses out on other dangerous problems. Refer to the associated papers for example lists that you can use as an overview to create a list that is personalized for your office.
They additionally show what an earlier inspection group focused on and also what locations it did not inspect. Do not simply repeat or duplicate previous examination results.
The Economics Of Racking Protection: Cost Vs. Benefit Analysis
Before doing a work environment examination, examiners must come to be aware of any kind of potential health and wellness as well as security concerns or patterns determined with other kinds of records. The adhering to describes other kinds of records: Ongoing evaluations Danger reports Case and examination reports Examination compliance orders Pre-operation checks Pre-start engineering health and safety and security testimonials Work danger evaluation (JHA) Periodic inspections (precautionary upkeep) Tracking device data (job-related health) Inner as well as outside audits Health and wellness summaries: Supervisors and employees ought to carry out ongoing evaluations as component of their work obligations.