copyright Occupational Health And Safety Regulations
Table of ContentsRacking Safety And Warehouse Efficiency: Striking The Right BalanceThe Top Cnesst Compliance Challenges And How To Overcome ThemRacking Protection Tips For Warehouses In Harsh EnvironmentsThe Role Of Racking Maintenance In Extending Equipment LifespanA Day In The Life Of A Warehouse Compliance Inspection OfficerStreamlining Cnesst Compliance For Large Warehouse Operations
No issue exactly how well performed, an assessment will only be rewarding if the worries noted by the team are very carefully examined and also ideal rehabilitative activity is taken. The reporting and the skill degrees of the individuals given this responsibility will certainly vary from one organization to the next, but it is very important to bear in mind the adhering to points when appointing responsibility for examining evaluation records.At the very least one of the individuals in charge of assessing examination records need to have the authority to take or determine the required rehabilitative actions and also to hand over that authority, as appropriate. Certain concerns may call for the viewpoint of a professional, such as a designer or an industrial hygienist. It is important to inform those doing the evaluations of any follow-up steps that are to be taken, in order to enhance their inspiration.
It is just as essential to make sure that those who are responsible for doing examinations receive timely comments. Clearly, if there is no responses or demo of rate of interest, they will promptly end that assessments are a meaningless exercise. Information acquired from routine examinations must be subject to a detailed analysis in order to identify which locations are in requirement of general rehabilitative procedures, and to recognize patterns as part of the efficiency auditing program.
7 Warehouse Inspections You Need To Carry Out
Anyone in charge of executing job place health and wellness evaluations, particularly function location health and wellness and security board participants and also representatives, will discover it valuable.
Health and wellness and also safety and security boards can help plan, conduct, report as well as display evaluations. Routine work environment evaluations are an important part of the overall job-related health as well as safety program and administration system, if present.
g., engineering controls, management controls, policies, treatments, personal protective devices) fulfill regulatory and also management system demands Planning is important for an efficient examination. Every inspection must examine who, what, where, when and exactly how. Pay particular focus to products that are or are most likely to become hazardous or undesirable conditions since of anxiety, wear, effect, vibration, warm, rust, chemical response or abuse.
Warehouse Compliance Inspection: How To Get Ready And Stay Compliant
Consider all workplace elements the people, the environment, the equipment, the products, and the procedure. People consist of the variety of employees, demographics, shift schedules, as well as guidance. Environment consists of the office structure as well as setting, and the conditions that border the employees such as sound, vibration, lighting, temperature, and ventilation. Devices includes equipment, devices, and also apparatus for creating an item or a service, along with security tools as well as personal safety devices (PPE) that might be called for.
Refine involves exactly how the employee engages with the various other aspects in a series of jobs or operations. Risks can occur because of hazardous work environment problems and practices including the office elements. Sorts of office hazards consist of: Safety and security risks such as those brought on by inadequate machine guards, hazardous power (mechanical, electrical, gravitational, pneumatic, etc), cars, equipment , devices , absence of loss defense , constrained areas , as well as housekeeping .
Chemical dangers caused by a strong, liquid, vapour, gas, dust, fume. or mist. Ergonomic risks created by improper job approaches, incorrect hands-on product handling , as well as improperly created Securite des entrepots workstations, tools, and tools. These area physiological (recurring and also powerful movements, uncomfortable postures, overwhelming) and psychological (work, time stress) needs on the worker that can bring about bone and joint injuries.
The Long-term Benefits Of Proper Racking Maintenance
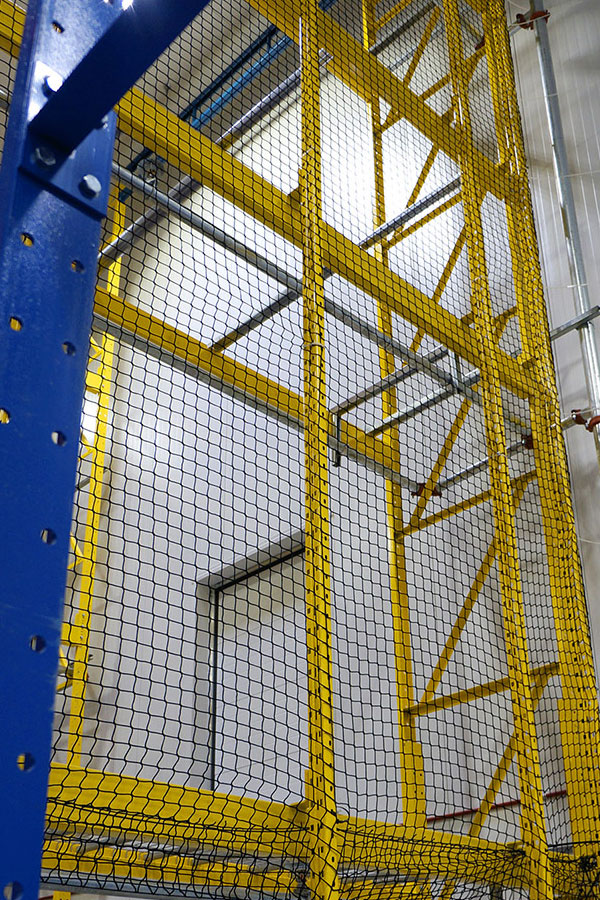

Check out workspace documents to end up being acquainted with the risks of the equipment. Recognize any kind of engineering safety controls called for to securely run the devices. Determine which products are used in the work environment and also whether safety and security information sheets are readily available. Find out if all sources of direct exposure are effectively regulated.
Demystifying Palettier Cnesst Regulations For Warehouse Operators
Check that all hazardous products are identified appropriately according to Work environment Hazardous Products Information System (WHMIS ) needs. These records include workplace policies, policies as well as guidelines, treatments, risk-free job methods, emergency action plans, records, as well as documents. Recognizing with the typical safe operating problems for the area can assist inspectors to identify risky variances.
Checklists assist with instant recording of findings as well as remarks however be cautious. Do not allow the evaluation team to end up being so aim on noting the information provided in the checklist that it misses various other unsafe problems. Use checklists only as a basic tool. Refer to the relevant documents for example lists that you can use as an overview to create a list that is tailored for your office.
They likewise reveal what an earlier examination team focused on and what areas it did not inspect. Do not merely repeat or duplicate previous evaluation results. Make use of the older evaluation records to aid try to find concerns, and after that identify whether suggestions were applied. Keep in mind if the modifications have worked.
Safety For Warehouses And Vehicle Maintenance
Prior to carrying out a work environment examination, examiners should become aware of any potential health and wellness and also safety problems or fads identified via various other kinds of records. The following describes other kinds of records: Ongoing examinations Threat reports Incident and examination records Examination conformity orders Pre-operation checks Pre-start design health as well as safety reviews Work risk analysis (JHA) Routine evaluations (precautionary upkeep) Tracking see post gadget data (job-related hygiene) Inner as well as exterior audits Health and wellness and also safety recaps: Supervisors and employees must carry out recurring inspections as component of their task obligations.